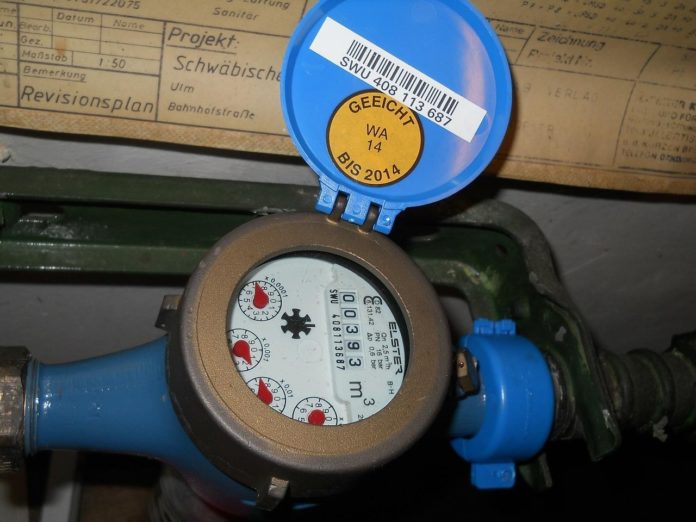
In the oil and gas market today, it’s always a challenge to keep stability between compliance, maintenance, and operations. At the same time, carrying out the production targets on both schedule and budget.
Oil and gas makers are put under pressure to meet strict and rigid environmental ordinances. Progressively, they’re looking for solutions for treating byproducts and produced water at the drill pad without becoming subject to the expense of off-site disposal.
A lot of technologies are utilized to gauge the circulation rate in oil and gas applications. The most common are differential pressure flow meters (DP), but they’re delicate to pressure changes. Coriolis counters might give accurate readings, but they can be expensive.
When ruggedness is needed, turbine flow meters are the best option. These counters can function well under any conditions. Read on to know more about turbine flow meters in oil and gas applications.
How Do Turbine Flow Meters work?
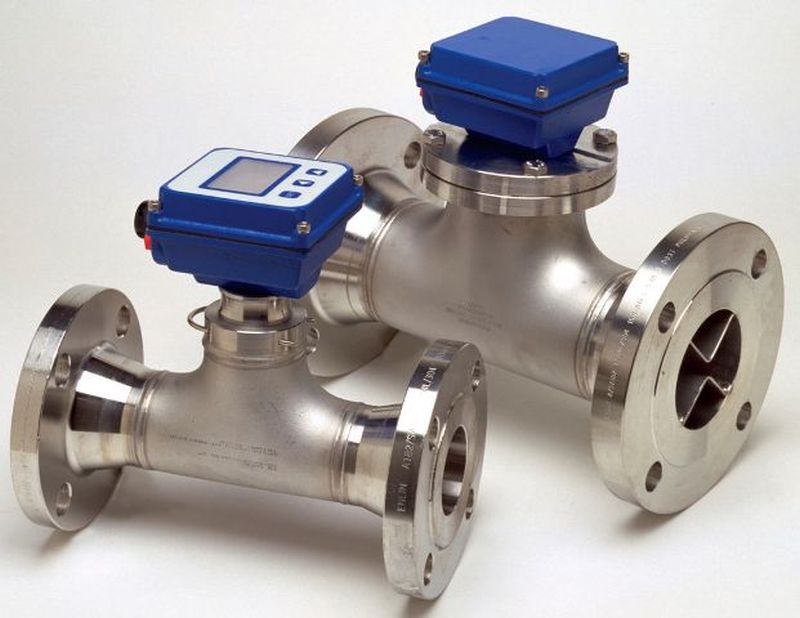
Turbine meters stand out or be excellent at measuring steady, clean circulations of low-viscosity fluids. In particular, those found in oil field environments. This technology keeps the mechanical integrity, and measurement accuracy in the abrasive, corrosive fluids generally applied in oil and gas production and other industries.
The fluid going into the turbine flow meter first traverses through an inlet nozzle with flow straightener. Thus, minimizing its unstable circulation pattern. Then, it circulates through the body, making the turbine rotor to spin at a speed relative to the velocity of the fluid.
An alternating current (AC) voltage pulse is produced as each turbine rotor moves past the magnetic field created by the magnetic pickup of the flow meter. The AC voltage pulses issue an output frequency that’s relative to the volumetric circulation.
Moreover, there’s a turbine counter that features rotor support, 316 stainless steel housing, journal bearings, wear-resistant tungsten carbide shaft, and CD4MCU stainless steel rotor. All these components aid the turbine flow meter to maintain mechanical integrity and high-accuracy when gauging abrasive, harsh fluids.
This turbine flow meter provides a reading accuracy of ±1% for larger ones. And a reading accuracy of ±1% over the upper seventy percent of the measuring range of smaller turbine counter models.
The repeatability of the turbine flow meter is ±1% and has a standard operating temp ranging from -101 C to 177 C (-150 F to 350 F). Plus, a turndown ratio of 10:1.
Industry Applications
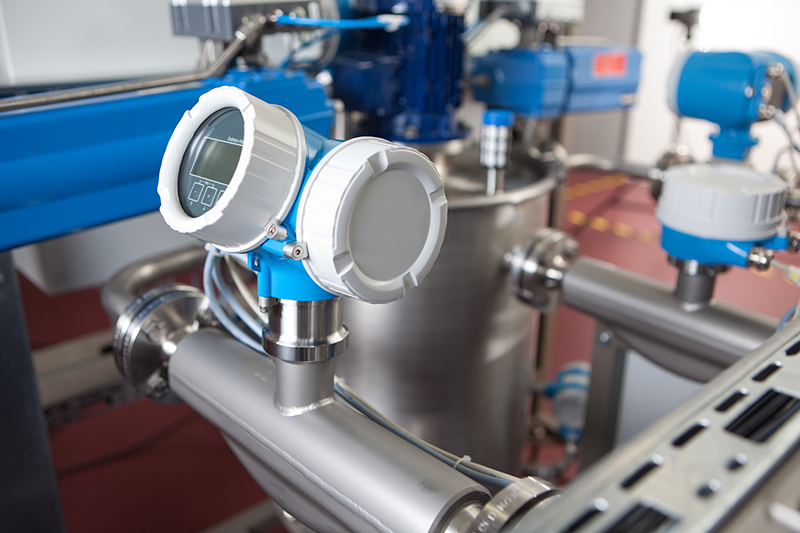
Turbine meters can gauge almost everything from liquids from wellheads, gases, to water in hydraulic fracturing operations. Common oil and gas industry applications for turbine flow meters include:
- Chemical Injection. Oil and gas producers need accurate and reliable mass dosing for oil and water treatment, pipeline, and downhole to maximize effectiveness and minimize chemical usage. Turbine meters are utilized to gas additives and counter liquid.
- Natural Gas Pipelines. This technology work in different pipeline installations, which includes those for offloading to smaller pipelines, chemical injection, and metering stations.
- Hydraulic Fracturing. Hydraulic fracturing for oil and gas wells needs durable and accurate flow measurement devices to monitor different processes throughout a treatment. Metering of reclaimed and used water is a chief application for turbine meters. Also, they can be utilized to monitor the chemicals and water applied to treat the water.
- Disposal Wells. In oil and gas wells, produced water is stored in tanks on-site or goes into the pit from where it’s trucked or piped to the disposal well sites. Or injected underground using high-pressure pumps for permanent storage. Remember that any disposal should follow the environmental regulations.
- Test And Production Separators. Test and production separators for product and well testing measurement, which includes those utilized for asphalt in oil sands operations, need accurate devices such as a turbine flow meter with a field monitor to gauge water-based fluids.
- Water Injection. Turbine flow meters can be used to measure process water recovered from and injected into wellheads. It helps get rid of the remaining scrub oil in older wells or keep fracking buildup pressurized.
Research and studies have shown that turbine meters are excellent in dealing with corrosive fluids and chemicals. Plus, particulate matter and high pressure in oil and gas production. Additionally, they can be utilized with heat trace and supplied with digital monitors.
Takeaway
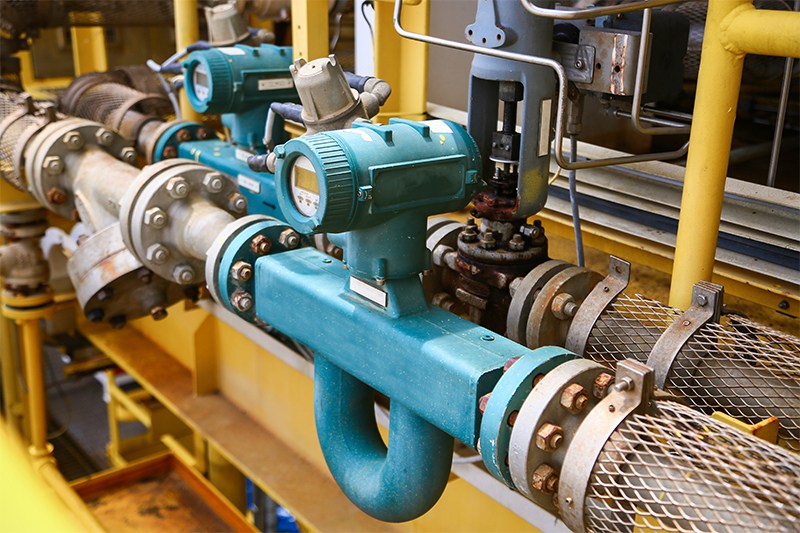
Turbine flow meters are easy to install, maintain, and operate. They are a cost-effective and reliable tool for obtaining or getting accurate flow data. Also, turbine meters are designed to minimize pressure drop and maximize output. Moreover, this technology can maintain high circulation rates over a wide range and provide pulse output that is linear to the flow rate. You can also check SmartMeasurement for more information.
Without a doubt, oil and gas producers can leverage the most detailed, accurate flow data possible with a turbine flow meter. These offer repeatable and highly accurate measurements of some chemicals, water, and oils with a low-cost of ownership.