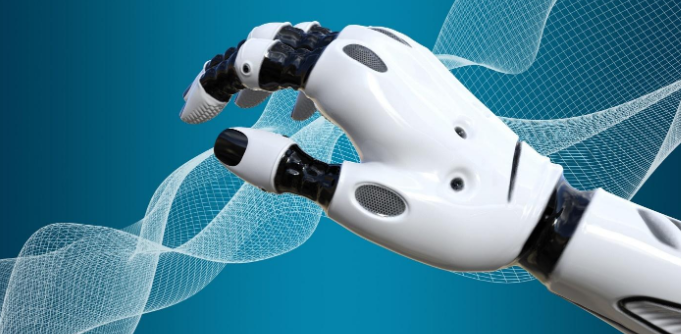
A robot can be regarded as a machine that resembles human beings. It can duplicate certain human functions electronically with the help of a computer. This means that its motion is computer programmable which makes it controllable.
Robots perform various tasks making human beings’ work easier:
- They can go through uncomfortable and dangerous physical conditions
- They can operate even in places where there is limited or no air
- They can do boring repetitive tasks
- They can carry heavy and sharp-edged objects
Each robot consists of separate robotic joints, which you can read more about at rozum.com. These joints make the robot to act similarly to human beings due to their relative movements. The connection of these joints helps the robot to move materials, tools, and devices during their performance of a variety of tasks.
Some robots have such a high safety rating that they are allowed to work hand-in-hand (or better to say gripper-in-hand) with humans. They are called collaborative robots or cobots. Here you can check joint details and characteristics for robots.
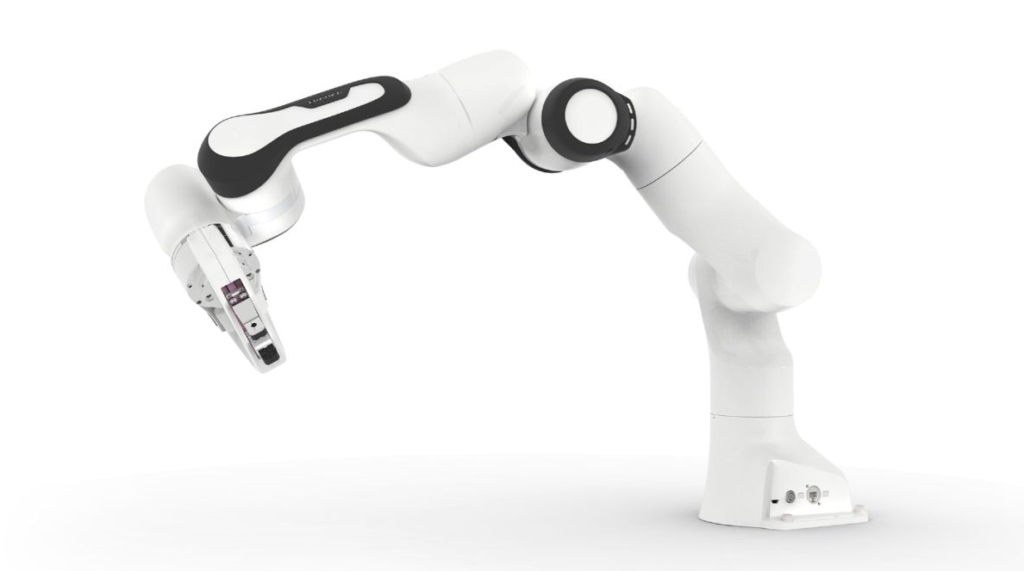
These are five main types of robotic joints:
1. Linear joints- linear joint can be designated by its letter L- meaning it can perform both translational and sliding motions. For this joint to achieve its linear motion the links should be arranged in parallel axes. They are also known as prismatic because their cross-section is referred to as the generalized prism.
2. The Orthogonal joint-This joint in some way resembles the linear joint. The only difference is that its input and output links move at right angles as they are perpendicular to each other.
3. Rotational joint- rotational joint can be regarded or represented as R-joint. As its name suggests, the rotational joint will allow the joints to rotate along the axis. The rotary motion can be vertical to the arms axes or perpendicular to the input and output links axes.
4. The Twisting joint-Twisting joint can be represented as the T-joint. This joint makes twisting movements amid the output and input links in a robot. During the twisting motion, the output link axis of the joint will be vertical to the rotating axis. The rotation of the output link is due to its relation to the input link.
5. Revolving joint- revolving joint can be referred to as the V-joint. In the revolving joint the output link axis stays perpendicularly to the rotating axis whereas the input link is parallel to the rotational axis. As in the twisting joint, the spinning of the output link in the revolving joint is due to its relation to the output link.
With these joints, the robotic arm can perform multiple industrial tasks like welding, handling of different materials, painting and many other applications.
Now let’s have a look at some Classifications of robots
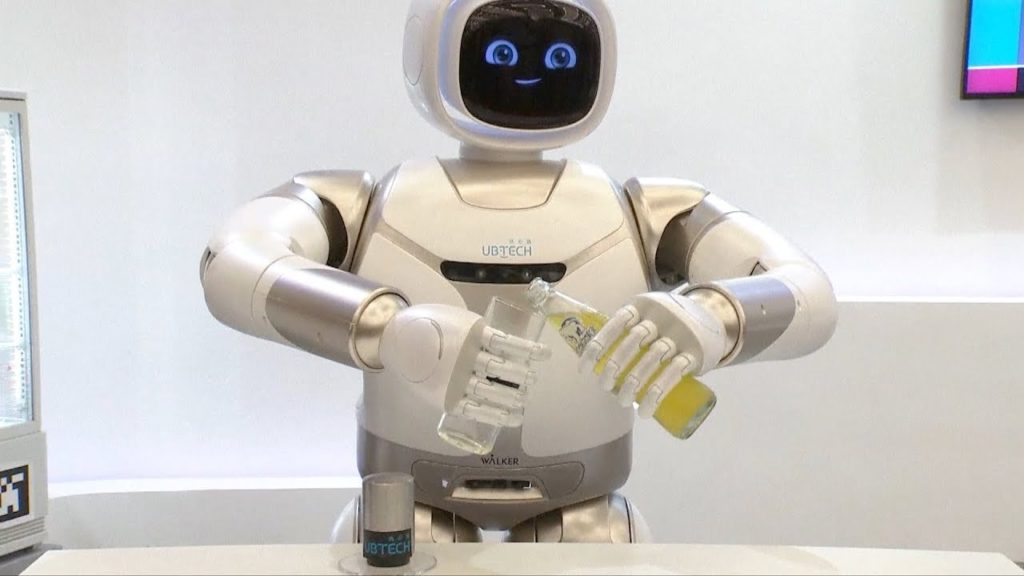
Based on physical configuration there are the Cartesian, cylindrical, polar and joint arm configurations.
Cartesian robots have links connected by linear joints and they have certain advantages:
- They have a great ability to do straight line intersection into furnaces
- Are easy to compute and program
- They have a good and rigid structure for a given length
Despite the advantages they also have some disadvantages:
- Due to its straight-line intersection, it can only reach the front of itself
- The Cartesian robots require large operating volumes
- Their axes are hard to seal
Cylindricalconfiguration robots have one rotary (R) joint at the base and linear (L) joints that help to connect the links.
Advantages;
- Due to its cylinder-like form, this robot can reach all-round itself
- Its rotational axis is very easy to seal
- It has a relatively easy and efficient programming
- They can be able to handle heavy loads having got a big working space
Disadvantages;
- It’s hard to cover its exposed drives from dust and liquids
- Due to its cylinder-like form, this robot can’t reach above itself
- It’s hard to seal its linear axis
The Polar configuration robot has a working space which is spherical. The polar robot arm is connected to its base with a twisting (T) joint and rotary (R) and linear (L) joints follow.
Advantages;
- A Polar robot has a large working environment
- Its two rotary drives can easily be sealed against liquid and dust.
Disadvantages;
- They have a very low accuracy
- A Polar robot has complex coordinates which are difficult to anticipate, control and program
When the cylindrical and articulated configurations are combined they form the jointed-arm configuration robot. The robot’s arm is attached to the base with a twisting (T) joint. The links that are in the arm are connected by rotary (R) joints. This is the most common configuration of many commercially available robots.
Classification based on the control system
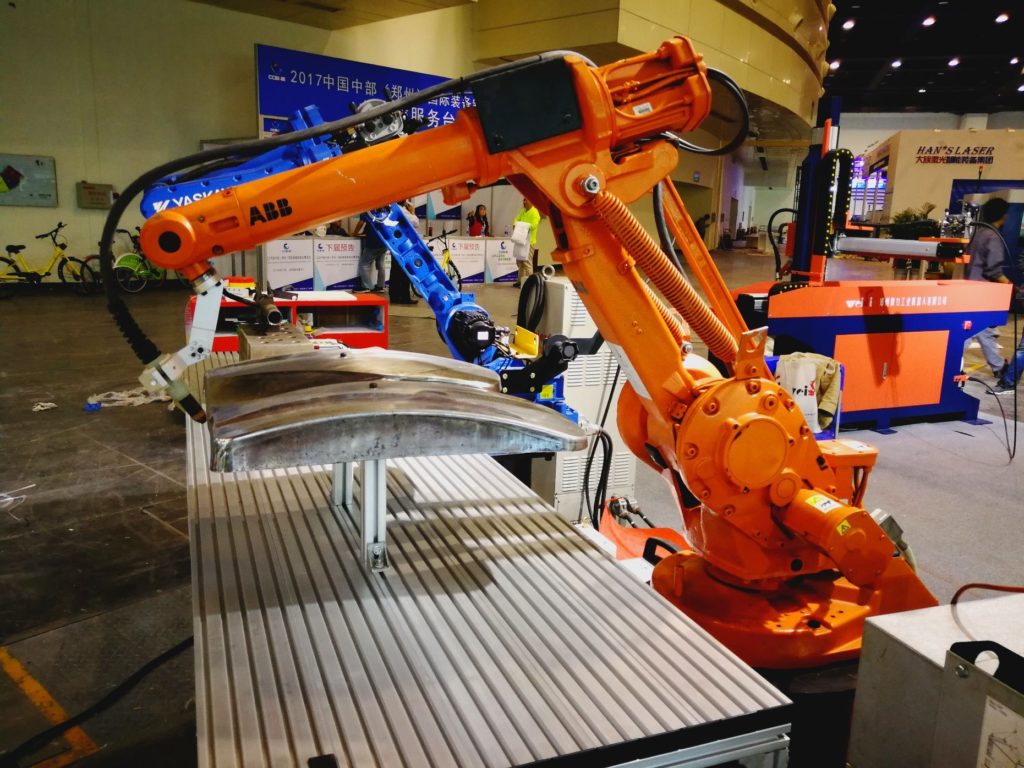
1.Point to point control robot
The point to point control robot has the capability of moving from one point to another. The robot locations are well recorded in the control memory. These robots cannot control the path to move from one point to another.
2. Continuous path control robot
The continuous path robot is capable of performing movements in a controlled path, where the robot can stop at any point along the controlled path. All the points along the path a well-programmed in the robot’s control memory.
3. Controlled path robot
These robots the controlling mechanism can bring about different paths e.g. straight lines, circles, and curves with high degree accuracy. In these robots, it’s only the start and stops points and the path that is stored in their memory.
Now when you know more about different types of joints and robots, it’s time to choose one for your business.